Did you know that manual handling accidents account for 17% of all workplace injuries? As if that’s not enough, 7.8 million working days are lost due to occupational musculoskeletal disorders, which are a common byproduct of unaddressed manual handling hazards. Given the prevalence of these issues, it’s important employers and site managers step up their health and safety protocols, which is where we come in.
By the end of this article, you will be in a better position to conduct a dynamic and effective manual handling risk assessment, identify any relevant hazards and implement the appropriate steps to control them.
Here’s a glimpse into everything we intend to cover:
- Manual Handling at a Glance
- Understanding the Dangers of Manual Handling
- Conducting a Manual Handling Risk Assessment
- The Bottom Line
Manual Handling at a Glance
Before we get things underway, it’s important to ensure everyone here is operating from the same base level of knowledge – after all, we want this guide to be accessible to manual handling veterans and newcomers alike. To do so, we need to answer a very basic question…
What is Manual Handling?
What is manual handling? While this may seem like an obvious question, reestablishing what this fundamental practice entails will make sure you cover all bases when assessing the various associated risks and hazards later down the line. As they say, it is always better to overprepare than underprepare.
So, manual handling – this term refers to any physical action wherein the handler is supporting or transporting a load by hand or via bodily force. Every time an employee lifts, lowers, pushes, pulls, holds or restrains something, this is manual handling. From off-loading pallets from a HGV with a pallet truck to moving a wheelbarrow, many activities fall within this definition, and each has the potential to become hazardous under certain circumstances.
What Makes it so Hazardous?
The reason manual handling carries numerous associated risks is due to the nature of the activity. Frequently, it involves strenuous, repetitive action; the bearing of heavy, bulky and otherwise awkward loads, which require a great deal of care and technique to avoid injury. As we will explain in more detail later, one of the many dangers of manual handling is the development of a work-related musculoskeletal disorder (MSD).
Your Legal Obligations
No matter the industry, scale of operations or immediate working environment, employers are required to meet certain standards as set out in law. This legislative compliance is intended to protect all workers from harm, and is covered by the following trio of regulations:
- Health and Safety at Work Act 1974
- Manual Handling Operations Regulations 1992 (as amended 2002)
- Management of Health and Safety Regulations 1999
To cut through all of the legalese, allow us to simplify things. These laws stipulate that employers must put measures in place to eliminate hazardous manual handling wherever possible, conduct risk assessments for manual handling tasks that cannot be feasibly avoided and then also reasonably reduce the risk of injury.
Often these measures involve goods labelling, i.e., providing precise information about the weight of each load handled and where their heaviest side is located, particularly for those whose centre of gravity isn’t perfectly centred. Then there are environmental or operational changes such as new working patterns or site layouts, which can be implemented to improve safety and efficiency.
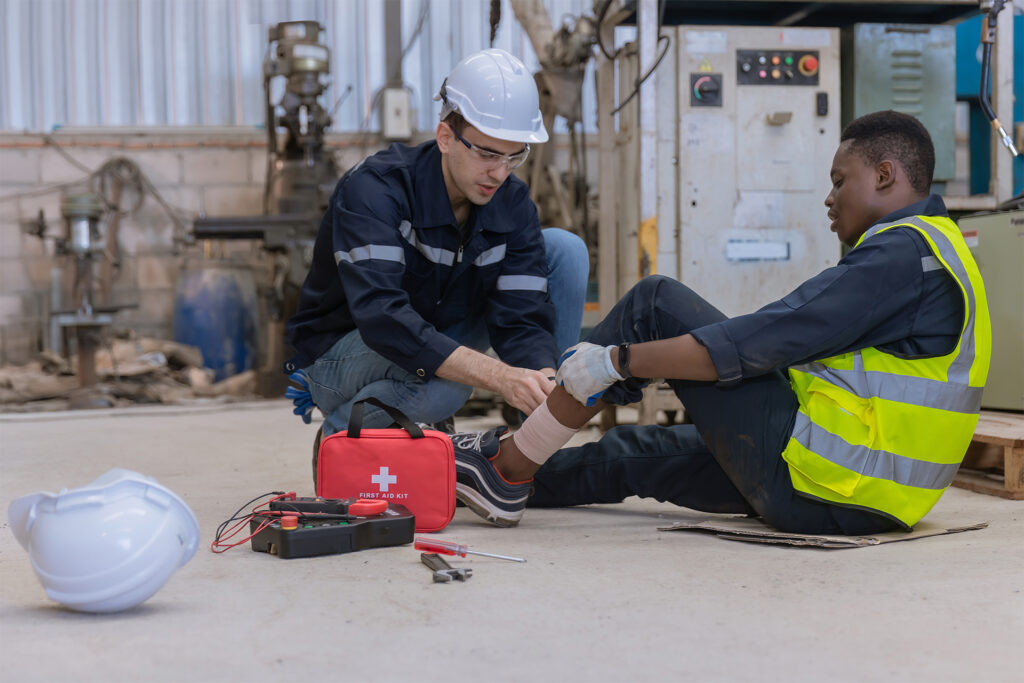
Understanding the Dangers of Manual Handling
As we’ve established, manual labour tasks carry a certain degree of risk to the workers conducting them; however, we’re yet to look at these risks in much detail. In this next part of the guide, we’ll share some of the most common ones to look out for and tips for identifying them, so you can mitigate issues as soon as possible.
Identifying the Risks
As a site manager or indeed any worker responsible for health and safety, it’s crucial you recognise the importance of site visits. Not only are they a great snapshot of your business’ operational performance, but they present the best opportunity for spotting any early warning signs when it comes to instilling the safety of both employees and visitors. By taking the time to liaise with everyone on-site and inspecting the premises regularly, it becomes much easier to identify any manual handling risks, such as those laid out below:
Short-term Injuries
If the proper precautions are neglected when handling heavy loads, workers can be subjected to a whole range of short-term injuries from minor sprains to bruising and cuts. Fortunately, with the right PPE and procedures in place, they can be greatly reduced.
Musculoskeletal Disorders (MSDs)
Work-related MSDs have been the most common type of occupational ill health in the UK for quite some time, with 543,000 workers suffering from them in the 2023/24 period alone. Musculoskeletal conditions present a particularly serious risk to employers and employees alike as they lead to early retirement, chronic pain and a significant limitation in mobility and dexterity.
These injuries are typically sustained from poor manual handling techniques such as incorrect posture or insufficient grip, but a lack of equipment and training are also major contributing factors.
Accidents: Slips, Trips & Falls
Another manual handling risk that must be accounted for is the potential for accidents such as employees slipping and tripping when transporting goods, or, in the worst case scenario, objects falling onto said employees. In certain industries, namely warehousing and distribution, this risk may be exacerbated further for those working at heights.
Damage to Goods & Equipment
Alongside the possibility of injury comes the potential for tools, machinery and other manual handling equipment to become damaged. Typically, these issues arise because of mistakes like handling the equipment improperly; for example, exceeding the weight capacity of a pallet truck with heavy loads, dropping inventory or applying excessive force.
Reduced Productivity
Finally, as a result of each of the previous risks mentioned, worker productivity and general operational efficiency can become significantly compromised. With increased absences due to injury and workplace trauma, prolonged equipment downtime and incident report write-ups on the table, the impact on both people and profit is pronounced.
Commonplace Manual Handling Hazards
Before we list some of the manual handling hazards you are likely to encounter regardless of environment, let’s pause for a moment. While indeed there are similarities across industries, the hazards tend to be situational and apply to a given contextual circumstance. Thus, take the following as general examples, and always be specific when conducting your risk assessment.
- Difficult Loads / Complex Tasks – It stands to reason that the trickier a load is to grip, manoeuvre and transport, the riskier the operation.
- Poor Working Environment – Whether an awkward layout, unnecessary obstacles, poor lighting, unsafe temperature or long distances to cover, the environment of the site can prove hazardous if not appropriately controlled.
- Insufficient or Faulty Equipment – Faults in equipment or a lack of machine capability poses a risk to employees, who may have to resort to moving loads via bodily force alone, or sustain injury during malfunctions.
- Individual Capabilities & Health – Individual capabilities also factor into the hazards, and may include health conditions, past injury or psychosocial issues.
- Lack of Education – A major manual handling hazard is insufficient or poor education/training as it might translate to poor technique, risk awareness and patchy procedure.
- Gaps in Organisational Procedure – In all workplaces where manual handling tasks occur, there must be an overarching policy in place, covering all aspects of health and safety, so staff know how to reduce risks and react in emergencies.
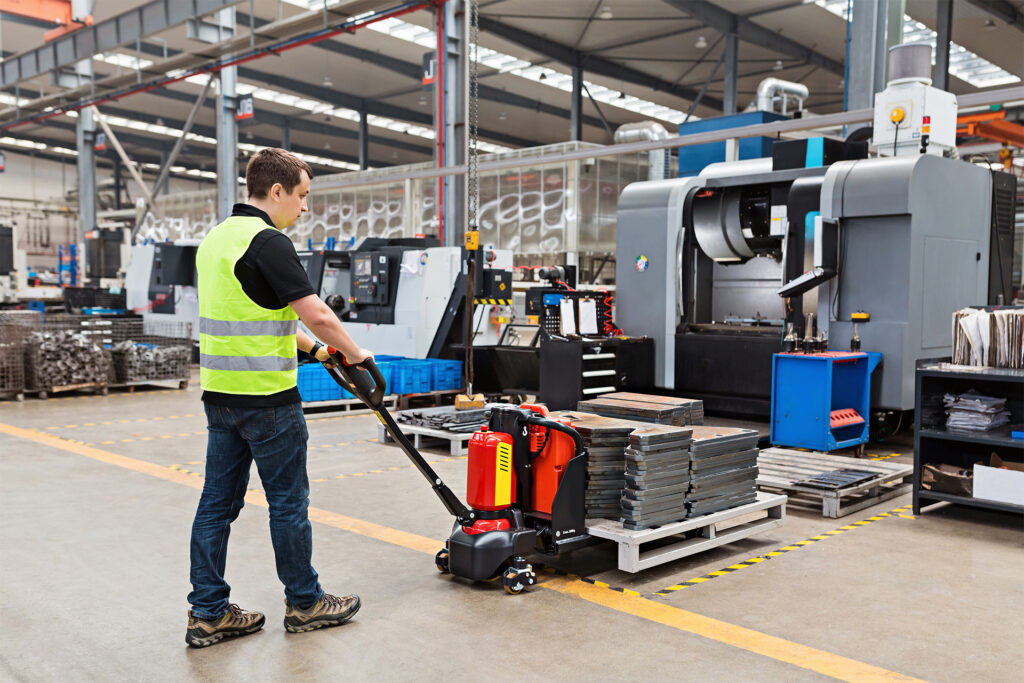
Steps for Prevention: 7 Manual Handling Control Measures to Implement
With the hazards outlined, addressing them with the appropriate action will be all the more straightforward. Below are 7 simple manual handling control measures that take into account the Manual Handling Regulations we mentioned earlier.
1. Limit Manual Handling Tasks if at all Possible
The first port of call when it comes to eliminating any risks is very straightforward; you should avoid hazardous handling tasks “so far as reasonably practicable”. Boiling this down, it means balancing the level of risk against the measures required to control it – i.e., the expense, time and trouble taken.
Therefore, you might wish to ask yourself these questions. Do you really need to move the object in question, or can you safely conduct the activity where it’s already located, thereby redesigning the task? Can goods be delivered directly where they will be used?
If you’re unable to avoid manual handling activities, this is when you should conduct a risk assessment and implement the remaining control measures.
2. Liaise with Stakeholders to Alter Loads
If loads are excessively bulky, difficult to grasp or are unstable when stacked, it goes a long way to make them lighter, more streamlined and safer to handle. This might involve changing the size of pallets so they’re easier to see over, altering the packaging type, or even providing handles that workers can easily grasp.
Of course, the process will vary depending on whether the goods are sourced in-house or externally, but nevertheless it’s helpful to arrange a discussion with the stakeholders involved to learn whether it’s feasible to modify loads.
3. Improve the Working Environment
This control measure encompasses a lot of details. Site temperature, humidity, layout, obstructions, floor quality, lighting conditions, wind and restricted movement/posture all play a role. To reduce each of the associated risks, you should ensure that the area is kept clean, well-lit, maintained and free of obstructions. This also involves providing suitable protective clothing or PPE, along with safe ways of traversing the site – uneven steps and steep ramps should be replaced with safer alternatives.
4. Upgrade & Invest in Effective Handling Equipment
Speaking of maintenance, an additional way to prioritise safety is via the use of compliant and high-quality equipment. For instance, are you able to automate the more hazardous tasks with machinery and robotics? Already using handling aids? Then, are they well-kept and suited to the tasks at hand?
Ideally, the devices used should be suited to the flooring type if they have wheels, possess a decent handle grip and provide an intuitive user interface. For instance, the best electric pallet trucks on the market enable employees to minimise fatigue, manoeuvre inventory in tight spaces more smoothly and avoid strain injury, all whilst keeping productivity and equipment downtime where you want them.
5. Update Manual Handling Policy
As per the law, when hazardous activities occur within a business’ premises, there should be a clear policy in place, which is communicated to all staff. On top of manual handling best practices, detailed information about the range of tasks and occupational health advice, you should also develop an emergency action plan in case of a significant incident. This contingency planning should cover how to handle casualties, remove people from danger, deal with emergency services and protect property.
6. Provide Sufficient Training to Staff
This manual handling control measure underpins much of what we’ve already discussed. By providing a sufficient level of training, including refresher training, all staff from junior workers to managers will feel more confident in themselves and be able to perform at their best. This may involve general health and safety guidance, or even bolstering inspection systems for handling equipment like pallet trucks.
7. Alter Organisational Procedure Such as Working Patterns
The final way to minimise manual handling hazards within your operations revolves around your work organisation. Consider the answers to the following:
- How is your manager-worker communication?
- Can the work be made less repetitive?
- Would revising shift patterns increase efficiency?
- Are you involving labourers in decisions that concern them?
- Are deadlines/workloads realistic?
- Can you find ways to make the most of workers’ skills?
You may find that in mulling these things over solutions begin to present themselves.
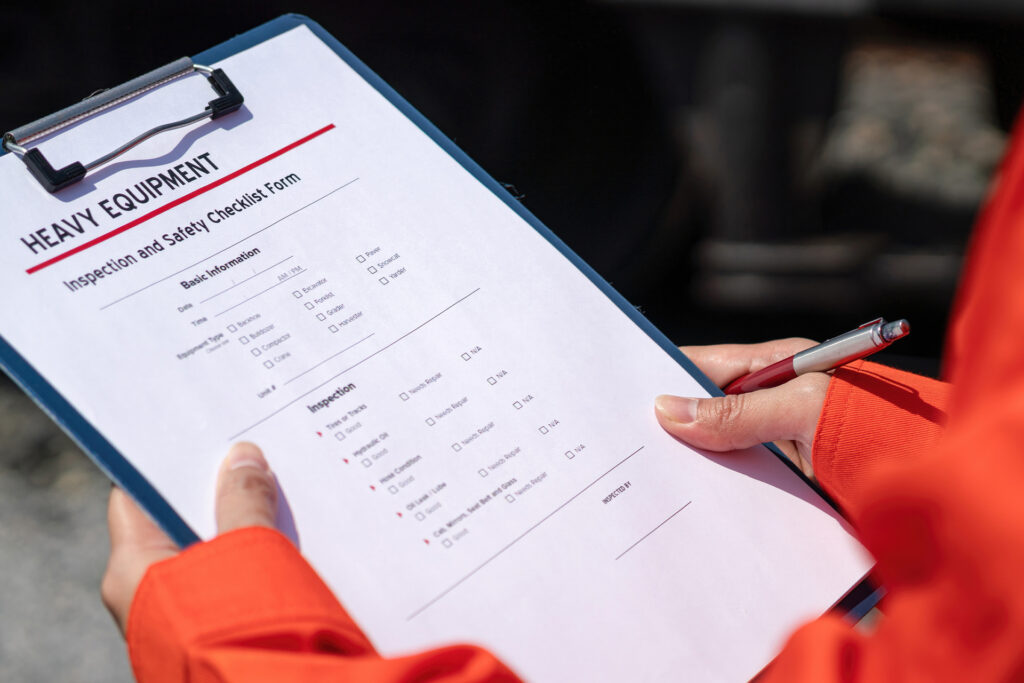
Conducting a Manual Handling Risk Assessment
Now it’s time to apply everything you have learnt thus far. When you conduct a manual handling risk assessment, you need to hit all of the following:
- A clear record of who could be harmed and how (refer to the risks we discussed earlier);
- Which control measures are currently in place;
- Further control measures you ought to implement;
- Who is responsible for carrying out those measures;
- And a realistic timeline for executing them.
For more in-depth information, we suggest checking out some of the specific resources provided by the HSE. Here are two we highly recommend.
- The Manual Handling Assessment Charts (AKA the MAC Tool), which covers lifting/lowering, carrying and team handling operations.
- The Risk Assessment of Pushing and Pulling (AKA the RAPP Tool) – this is specific to pushing and pulling operations.
The Bottom Line
While the next steps for site managers will assuredly vary across industries and indeed within the same sectors, one thing is for certain: your manual handling risk assessment should contain all of the hazards discussed in this guide, and more. Remember, each facility’s operations will look different – distinct layouts, sizes, load types and employee organisation all presenting different requirements – thus, it’s critical that the control measures you implement are tailored towards your unique circumstances. Here, cookie cutter solutions simply won’t do.
Nevertheless, by heeding the risks we outlined previously, looking out for early warning signs and implementing the right corrective action, making your premises safe as possible is not only achievable but fairly straightforward too. So, whether you’re undergoing a complete rehaul of your operations, or simply making a few tweaks here and there, we wish you luck!
Still feeling curious about how handling aids and equipment can optimise your operations? Our friendly team is happy to answer your queries via email. In the meantime, though, why not explore the rest of our blog for further insights?